With ridesharing and autonomous vehicles, user preferences for the position and angle of a seat will travel with passengers as information in an app, and the seat in a car someone has never been in before will automatically morph as he or she enters the vehicle. The relationship between car and rider will no longer be long-term. As modular interior design becomes the norm for a new breed of cars, seats will have to travel farther and faster.
Automotive interior engineers will depend on advancements in shaft design to enable this increased mobility, and specifically on next-generation flexible shafts. From the first expected major changes, such as partially autonomous driving, rider demands will change. Once the driver no longer needs to control the accelerator and brake so closely, she or he will desire more leg room.
In current power seating constructions, flexible shafts turn at between 2800 and 3500 rpm. To accommodate future modular interior designs, these speeds reach approximately 6000 rpm. Some shaft designs exist today that can accommodate this acceleration, but these components produce an unacceptable level of noise when in operation. The simple engineering solution, to enlarge the outer diameter of the shaft, requires the redesign of all interfaces, including the motor and gears. Automotive manufacturers act largely as component integrators, and prefer not to make such major alterations to systems, so this option fails to meet the expectations of the market. The challenge for S.S. White: Create a shaft that performs at the same noise level as current shafts, can replace current shafts one-to-one in power seat constructions, and achieves double the speed.
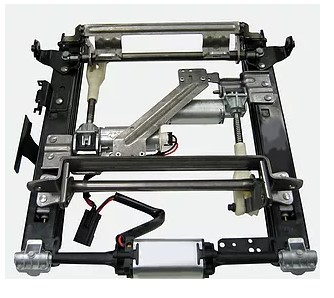
For the flexible shaft experts tackling this design challenge, the main focus is material. The basic flexible shaft for seat movement is made of layers of carbon steel wire wrapped around a core, with an outer layer of nylon flock yarn. The flexible shaft is then covered in tubing. What is the best material for the flexible shaft, the shaft coating, and the tube that houses the shaft? S.S. White engineers use a variety of tools to pursue this R&D goal, namely industry-leading computer modelling. The engineer-owned organization also performs in-house design, manufacture, and lifecycle testing for rapid versioning. By adjusting material and design, the company is on track to deliver flexible shafts meeting automotive industry requirements that perform at three times the speed of current power seating shafts.
As technology marches on toward increased vehicle autonomy and ridesharing, fast seat movement will become an increasingly critical component in the creation of a positive rider experience. To meet this demand, careful material design by S.S. White’s top flexible shaft engineers will unlock new flexible shaft speeds and therefore seat movement rates.
ANALYSIS
This article goes over the issue of material within seats, typically heavy weighted, difficult during moving, also slow and typically loud. Moving seats in, out and around the car is an inconvenient and uneasy task for nearly everyone. Which poses a real problem for the future autonomous vehicle, where creators hope that users will be able to customize the interior of their car so that it best fits their needs and functions. The article also then goes into explaining a new type of material being used for seating, to make them lighter weight and therefor easier to move. Overall, most directions for rethinking the car are considering material changes and improvements, this is something I certainly also want to consider and understand while making my own concepts. Understanding material possibilities will help a lot in building a design that functions as it should, and can also be explained as to how. Materials are super important to the future of all these car concepts, as they are the literal building blocks of everything hoped to be achieved.