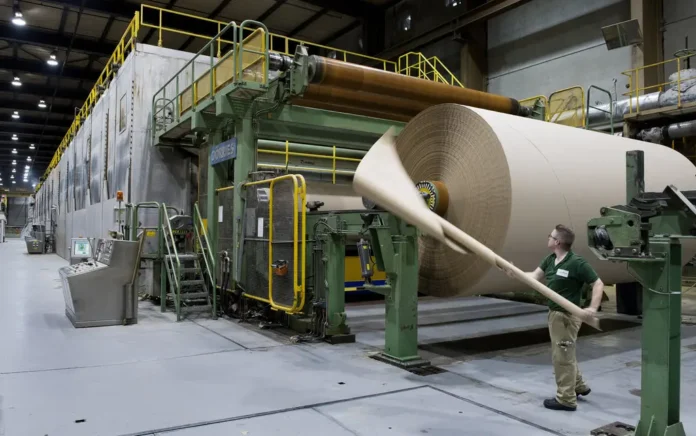
ROERMOND, The Netherlands — Three times a week, tanker trucks make an hourlong journey from a baby-food factory in Nunspeet, in the central Netherlands, to a paper mill in the southeastern city of Roermond (Schuetze, 2014).
The trucks carry 90 cubic meters, or about 24,000 gallons, a week of phosphate produced as a waste byproduct at the baby-food factory, to be fed to bacteria in an anaerobic fermentation tank at the mill. One person’s trash can be another’s treasure. “They had a lot of expenses to get rid of it, and we had expense to get it, so we are both happy,” said Mark Nabuurs, the manager of innovation and development at the Roermond plant (Schuetze, 2014).
Mr. Nabuurs and other executives at Roermond Papier, a unit of the Smurfit Kappa packaging company, based in Dublin, cite the phosphate deal as an example of the company’s commitment to the idea of a circular economy. In a traditional linear economy, products are made from raw materials and everything — byproduct waste and product alike — ends in the scrap heap. In a circular economy, the product is made from recycled materials and ends up being recycled itself (Schuetze, 2014).
“The linear economy is at an end. I really believe it is over,” said Jo Cox, the general manager of the Roermond plant which, in an industry once associated with water pollution and deforestation, has won several environmental awards over the years (Schuetze, 2014).
The mill makes brown packing paper exclusively from recycled and alternative fibers, and it has made changes to its production processes, its supply chain and its waste disposal practices to reduce its environmental footprint. It currently produces less than a kilogram, or 2.2 pounds, of solid waste for every metric ton of paper that it makes, converting combustible waste into fuel pellets that it sells as a byproduct to other industries. It uses natural gas and biogas to generate power and steam (Schuetze, 2014).
It uses just 2.7 liters, or 0.7 gallons, of water to produce a kilogram of paper, less than 2 percent of the volume needed to produce the same amount in a conventional mill: The water, drawn from a nearby river, is recycled several times, and cleaned by organic processes before being returned to its original source (Schuetze, 2014).
Personal notes:
Learning about materials implies knowing that other alternatives must be implemented as a first step to mitigate the impact on the environment of the current model because, realistically, the process of adaptation and change to new materials will take time. Therefore, initiatives such as those used in the Mill factory demonstrate how production as necessary as paper can be done with less impact. The company is more efficient and remains competitive.
Schuetze, C. F. (2014, November 18). The circular economy of recycled paper. The New York Times. Retrieved January 22, 2023, from https://www.nytimes.com/2014/11/19/business/energy-environment/closing-the-loop-on-recycled-paper.html?searchResultPosition=1