Author: Roshni Iyengar
Date: Mar 12, 2018
What makes the show go on.

An unforgettable world tour like U2’s 360 degree tour or The Rolling Stones’ A Bigger Bang is put together by the efforts of hundreds of people, right from artists and managers to roadies and logistics staff. The elaborate stages, lights and other equipment, constitute the skeleton of these larger than life performances. They too travel the world with the artist over the course of the touring period.
Logistical feasibility is one of the major deciding factors of creating a tour schedule. Even the legendary rock band KISS didn’t tour in Australia until 1980, because it wasn’t logistically cost effective enough for them in the 70’s.
Taking the show on the road
Entertainment Logistics is a very organised and controlled space. What differentiates it from regular freight, is the lack of room for delays, damage or errors in scheduling. Every piece of equipment transported is paramount to the show. For cargo companies specializing in tour logistics, the planning starts with site inspections of the tour locations.
The best mode of transportation is then charted out for each of the venues, according to the equipment needed. The bigger the act, the more the equipment that needs to be transported. Most artists travel with their own audio, lighting, video, maintenance, & even catering equipment. The elaborate stage sets also need to be built, dismantled, packed & transported from venue to venue.
U2’s 360 degree Tour employed 120 trucks to move the stage, the screen, the lights, the 250 speakers and more from venue to venue. Beyoncé’s Formation tour of Europe, needed 7 Boeing 747 cargo planes, to transport all the stage equipment across countries.
These cargo companies handle everything from imports, exports, customs and carnets for the tour schedule, using trucks, air and sea freight.


Special trucks which have padded walls and nooks to protect the equipment are used. For air freight, newer aircrafts have weight restrictions and smaller doors and hence, often unsuitable for band logistics.
When the equipment arrives at a venue, it is set up in a predetermined sequence- rigging, stage set, lighting, video, and audio. The band gear is often the last to be brought in, and after the show everything is packed in reverse.

For concerts having elaborate stage sets, like U2’s 360 ° Tour, artists usually have two exact sets of gear (U2 had 3) traveling the country. This way, when a band is setting up a show in city A, the other crew is en route to the city B, already setting up for the next show.
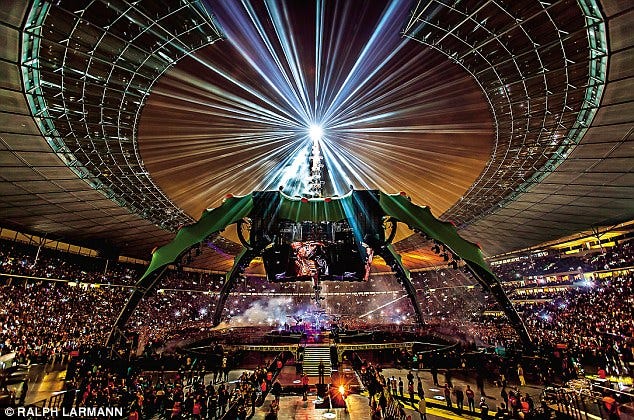
Time is of the essence
For international tours, the success of a show hinges on the smooth and timely clearance of the band’s equipment. The biggest logistics challenge that artists face is getting their equipment across international borders. An eight hour customs delay once caused Australian rock band Tame Impala to cancel their show in Germany. Anything from incorrect paperwork to a customs agent in a bad mood can delay band gear in transit. Hence, cargo companies often employ customs specialists and try to set up the customs clearance and airport transfers well in advance.
Moving the People
It is not unusual for concert tours to have crews of over 100 people. The core staff includes riggers, carpenters, caterers, security, technicians, electricians and drivers. All the support staff and their equipment has to be moved, while making accommodations and food arrangements. On Bruce Springsteen’s Wrecking Ball tour — a team of over a 100 people took care of logistics. Paul McCartney has a support staff of 130 people while on tour, including his own team of vegetarian caterers!

Expecting the unexpected
Logistics companies are often given a lead time of 3–6 months to route the artist’s cargo. However, bands and artists often add venues and festivals during tours which have to be fulfilled with a little as a week’s lead time.
Rock-It Cargo- a tour specialist freight forwarder once packed and loaded gear for The Police from Singapore to Macau in a little under two hours. Ed Butler, their VP stated- “We built 30 pallet positions — more than 154,000 pounds — on a Singapore Airlines Cargo 747 freighter in one hour and 40 minutes. That was from the time the first truck back in, to the time the last pallet was weighed. And then we were gone.”
Challenges like this are overcome because of the logistics company’s familiarity with the band’s equipment and ensuring smooth paperwork for customs.
Comments:
Concerts have become increasingly more elaborate and costly. With hundreds of staff going with artists and months of preparation it can be extremely stressful and costly. I think it would be very beneficial to either have a 3d printer going on tour with artists or venues have their own 3D printers at either stadiums or large stages.
This article really puts an emphasis on timing. Everything has to be working like clockwork. If something breaks or you want something new to make it would be great to just print it.
International tours have more problems, having to transport massive amounts of equipment overseas costs thousands. Beyoncé’s tour had 7 747 jets. At an average fuel cost of $19,150 per hour. So her 7 jets going from NYC to London would cost $930,000 just in fuel. Being able to 3D print some of these props will cut down on transport costs.