Author: Glenda Taylor
Date: 04/04/2022
Founded in 1976, Habitat for Humanity has constructed hundreds of thousands of affordable homes for people who need them. Now, using automated computer technology and a patented concrete mix, Habitat for Humanity recently completed its first 3D-printed house in Williamsburg, Virginia. The house’s new owner, April Stringfield, and her 13-year-old son are excited to move in and make the house a home.
While 3D-printed homes are still relatively rare, the successful completion of the Williamsburg house is a testament to the growing desire to build affordable homes while conserving natural resources like trees.
It’s a Regular House
Although the walls of the Williamsburg house were printed rather than stick-framed, the home is still just a regular house. In 1,200 square feet of living space, it includes three bedrooms, two full bathrooms, and a covered front porch where Stringfield can enjoy warm summer evenings.
The contractor incorporated traditional siding on the roof gables and used standard bricks on the porch pillars. In addition to the house, Stringfield received a 3D printer that will allow her to print cabinet hardware and light switch covers.
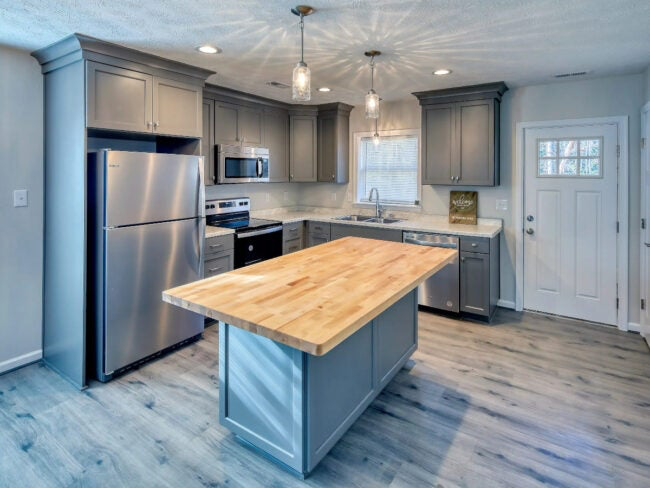
3D Printing Saves on Construction Costs
During the pandemic, some building material prices doubled or tripled primarily due to supply chain issues, which subsequently drove up homebuilding costs. By using concrete rather than wood, Alquist—the contractor that printed the walls of Stringfield’s new home—saved Habitat an estimated 15 percent per square foot.
While homebuyers do not pay for the labor needed to construct a Habitat home, they do pay for the cost of construction materials. In this way, the money saved on material costs is passed on directly to the buyer.
The Printing Process and Color Selection
It took just 28 hours to print the concrete walls of Stringfield’s home. Alquist uses a patented concrete mix and impressive-looking extrusion machine to print exterior and interior walls, which are reinforced with steel during the printing process.
Afterward, the exterior walls are sealed with a clear or tinted coating that keeps moisture from transferring through the concrete. Homeowners can choose a standard gray concrete color or select from a range of attractive earth tone hues to give the home a custom look.
Traditional Construction is Part of the Process
After Alquist finished printing the walls, traditional builders constructed the roof, ran plumbing and wiring, and installed interior flooring and other finishes. Through the Williamsburg chapter of Habitat, contractors, subcontractors, and other volunteers donated their time to complete the remaining parts of the house.
Analysis:
If you haven’t read my post titled “Architects: The Problem With 3D-Printed Buildings,” go read that first. This is basically a direct response to the concerns raised in that article. There, they said 3D construction printing cannot replace the many materials and processes need to construct a building. In this article, Habitat for Humanity is basically replying, “You’re right.” To make this house, they use 3D printing only for what in makes sense for, and nothing more. It efficiently erects a foundation and walls, and the rest is done issuing traditional construction. The interior (and much of the exterior) looks like a completely normal house. In this example we can learn that there is not need to stretch a technology beyond what it is ideal for. Leverage its strengths and simply look elsewhere for the features of a product that require something else.
Source: https://www.bobvila.com/articles/habitat-for-humanity-3d-printed-home/