Article posted 7/26/21
Swiss public research university ETH Zürich has teamed up with Zaha Hadid Architects to create a new type of bridge that uses less material and enables new types of forms.
By 3D printing concrete at specific angles, the collaborative team was able to produce blocks with layers “orthogonal to the flow of compressive forces,” allowing them to design differently-shaped blocks for different portions of the bridge.
On-site these blocks are fitted together in the manner of traditional stone arches—i.e. the structure is self-supporting—but the arrangement allows for wildly organic shapes that no traditional stonemason could ever hope to work out on paper
The blocks stick together through gravity, meaning no mortar is required. No steel reinforcements are necessary, either. And if needed, the entire bridge can simply be disassembled and reassembled elsewhere.
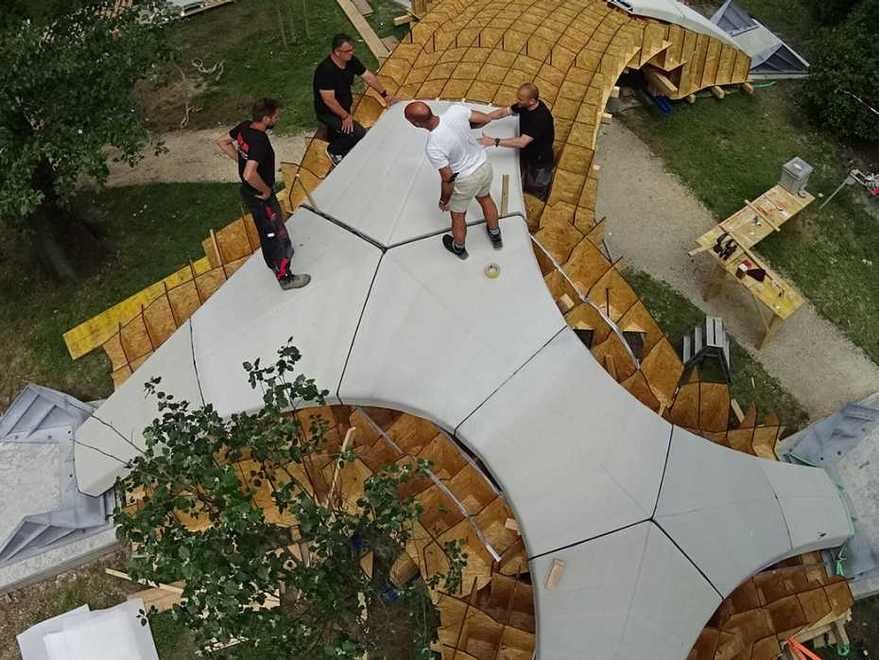
However, as with 3D printing certain forms in plastic, temporary support is needed. In this case, a rather comprehensive OSB scaffolding has been erected, with the parts having undoubtedly been cut with a CNC mill. This should offset the resource savings somewhat, but we assume that on-balance, they’re still in the black.
Analysis
This article was interesting to me because of its creative use of interlocking components. 3D printing can be tricky when it comes to elevated or lofted parts so I thought it was intelligent to pre-fabricate the concrete parts and put them together on site. This requires a certain level of planning and problem solving.
Although I do not know what my final project will be yet, I want to keep an open mind about the structure’s form. Perhaps there is room for negative space.
Take-Aways
Concrete may seem hard to work with when it comes to overhangs and arches, but pre-fabrication and creative problem solving can help create ways around it.
Concrete does not have to be bulky, it can be elegant and innovative.